The View From Over Here: Teaching and Exploring Structural Engineering Practices From Around the World
Peer Perspective: Gian Andrea Rassati, Associate Professor at University of Cincinnati
Our team recently met with Gian Andrea Rassati, associate professor at the University of Cincinnati, to learn more about his perspectives on bolted connections, structural engineering around the world, and advice on becoming a structural engineer today.
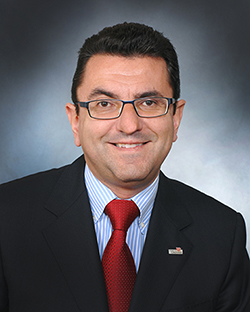
Q: Can you tell us about yourself and your current role at the University of Cincinnati?
A: I’m an associate professor at the University of Cincinnati and have been here for 20 years. I’m originally from Italy where I actually earned my degrees there. My Ph.D. was straddling the ocean. I worked at Georgia Tech on an experimental test during that time and eventually found my position here in Cincinnati.
Similar to other tenure faculty members, I teach classes, research and do quite a bit of service, both internally to the university and also to the engineering profession at large.
Q: Can you describe the coursework you teach as well as the areas of research you prefer to focus on?
A: My coursework is typically focused on the analysis side of structural engineering rather than the design side. I occasionally teach steel design, but the bread and butter of what I do are structural analysis courses for undergraduate and graduate students. I teach structural dynamics courses, earthquake engineering and finite element analysis courses as well. On occasion, I also teach a slightly different course that’s called Art Architecture and Engineering in Ancient Rome. That is a course for the honors college here that actually attracts students from all majors and ends with a 10-day trip to Rome and another city in Italy to reinforce what they learned during the class. You can’t be a great architect and know nothing about structures, or a great structural engineer and know nothing about architecture to create a work of art.
I have researched bolted connections, beam-to-column connections, welded connections, including a focus on the seismic behavior of structures. I’ve worked on lateral force-resisting systems development, focusing either on bare steel structures or steel-concrete composite structures. Occasionally, I have spent time researching bridges and their structural aspects as well.
Q: Can you tell us about any notable HSS project you’ve seen, worked on or studied?
A: You see pretty interesting HSS projects everywhere at this point in time, more so in the last 10 years in this country.
I’ve seen interesting applications of HSS on a trip for a conference in New Zealand, and that was almost 10 years ago. I’m always interested in seeing the different approach New Zealanders have taken on innovations in construction because they almost do the opposite of what we do here. We work here on new standards of specifications that will actually hit the desk of a design engineer in six to eight years before they go through a full cycle, then they get incorporated into the international building code, and then local codes incorporate them. However, New Zealand had a stream of earthquakes that hit 10 years ago, and they basically started implementing new ideas in practice almost before they were done testing them in a laboratory. They took the entirely opposite tack to this. I keep thinking that there must be some happy medium in between where we can actually do something quickly and make sure that everything is safe, but that’s the nature of the beast I suppose. HSS has been at the center of all these innovations.
Q: For engineers who are new to designing bolted connections, are there tips you typically like to share on common pitfalls you’ve seen?
A: Bolted connections are seemingly simple things, but there are a lot of aspects that need to be considered to properly design a connection. So, part of it is the fact that not many engineers will actually end up designing connections. A lot of the time, fabricators will actually perform the connection design at the end of the day while the engineers give them the forces for which those connections need to be designed. I understand that fabricators are the ones who know what the most economical approaches are and possibly the most appropriate approaches for a specific connection. But at the same time, I don’t necessarily like it because I would like the design engineer to actually have full control of the structural design. One thing I always try to stress to students and young engineers is that it’s always a good idea when you’re considering a specific connection to just give a ring to the fabricator and see what they think so that you can actually provide them with the best information.
Then going more into the nitty-gritty details, one would think that one of the easiest things is selecting the length of a bolt for a specific connection. That’s not as easy as it seems, and I can’t tell you the number of graduate students we had here who were designing an experimental project that ended up ordering the wrong bolt length, only to discover it when they actually tried to put all the plies together in the grip. They discover they don’t have enough threads or, even more commonly, they actually run out of thread and the bolt is still hanging without gripping anything. So, bolt length selection is probably one of the most under-considered things in bolt connection design.
Q: What are common challenges to bolted connections with HSS members? Do you have tips to assist engineers in overcoming these challenges?
A: The most obvious challenge is the fact that some connections with HSS members may end up being blind connections. You may not have access to the back of the joint. So, a lot of bolted connections become difficult because you either design them toward the ends of the member where you can actually reach in to access the bolts or you’re going to have to start providing access holes in the wall of the HSS. But then the design issue becomes whether you have enough HSS cross section to accommodate access holes, or you have to start thinking of welding or other solutions.
You may need to add flange plates that are attached to the outside of these tubes in order to provide connections. You may end up having to bypass the HSS entirely by having a plate that goes around and connects the other members to the plate that is then connected to the HSS. So, it’s more challenging because it’s an enclosed shape. You can’t really reach inside.
You have some blind bolt solutions. Some of them are certainly fine for bearing-type connections. But if you’re looking for pretensioned connections where the bolts are actually actively clamping the connections together and providing a normal force to the surfaces within the grip of the bolt, that becomes challenging. A lot of blind bolts really cannot be fully pretensioned and cannot reach the tension that standard bolts would actually be expected to reach. And so, pretensioned and slip critical connections are more difficult to achieve.
There are some solutions out there that seem more promising than others to solve the issues of bolting, and some are still somewhat requiring some access at some point in time inside the tube. I’m thinking of a proprietary solution Atlas Tube has recently been using. The other proprietary bolt configuration is a one-sided type of connection that allows you to actually do everything from one side and still have a reasonable amount of pretension through it.
Q: Through bolts are one alternative to standard bolts and bolted HSS connections. Do you have tips for engineers to keep in mind when specifying or designing through bolts including bolt length or ASTM considerations?
A: So, for through bolts, the biggest challenge on the mechanics side is the fact that you have a long bolt. The amount of torsional rotation a long bolt sees is proportional to the length of the bolt itself. So, a bolt that’s twice as long is going to rotate twice as much as a short bolt under torsion alone.
More importantly, there’s also the fact to consider that in some connections, you may end up already having some bearing forces that are active. Not all connections look like they look on a piece of paper or when you’re designing them where the bolt goes exactly through the middle of the hole, through the middle of the next hole, through the next plate and so on. So, there may be some effort involved in getting the bolt through, and the longer it is, the larger the tolerances will need to be. If you start hammering the bolt in place, then you’re running the risk of fouling up all the threads, and then you won’t be able to get the nut on. Even if you get the bolt in without ruining the threads, there’s a matter of actually applying a torque. If you can get to the nut and turn the nut, that’s fine, but if you’re trying to turn the head, then torque has to overcome the friction at the holes through the entire line of the connection. Through bolts are complicated. It can be done, but it needs careful tolerances for it.
Q: Our technical article for this month is on bolted end splices for round HSS in tension. What are common connections you’ve seen for bolted or welded HSS splices and what are a few considerations to keep in mind when designing them?
A: The design considerations are the same – speed of execution, cost of execution and availability of the means of execution that you have there. And of course, there’s the safety that’s underlining that whole idea — the fact that you want to have a safe connection in there. So, a lot will depend on the types of joints the erector is used to building as opposed to those with which they are not familiar. So, a lot of it is going to be local practices versus overall practices. And again, it depends where your erectors are. Is it a large company or a mom and pop shop?
The main discriminant between welded connections and bolted connections, at least to me, is the fact that welded connections are probably best done in a controlled environment. Typically, in a fabrication shop, they can reach the pieces without hanging somewhere upside down to try to make the connection. They are in their shop, and they can turn the piece however they want to actually get the best possible access. That’s the best assurance for good-quality welds.
The beauty of bolted connections is threefold. One is that you have the same level of quality of the connection whether you are in the field or in the shop because they’re relatively simple to do. You still need a specialized person to actually install the bolts, but as long as they follow the instructions, it should be easily performed and placed. Two is that bolted connections have the benefit that you can undo the bolt. You can undo the nut and take the bolt out if you need to replace something, which is a lot harder when you’re looking at welds. The third benefit is that it still provides you with a level of safety or level of structural performance you may be seeking.
Q: Originally, you received your structural engineering Ph.D. from the University of Trieste in Italy but now work for the University of Cincinnati. Are there any shifts in approaches or thinking that you’ve noticed between Italy and the U.S. when it comes to structural design?
A: There are a lot more similarities than you would think in design thinking. There’s the fact that there is a whole entirely different set of design specifications and requirements between Europe and the United States. And probably even more so the fact that the design standards have the strength of law in Europe as opposed to here, which are just something more than best practices. At the end of the day, they are similar because if you don’t meet the best practices, there can be consequences and you are held liable. But standards not carrying the full force of law also provide you with more freedom because if you can prove that what you’re doing is actually safer or as safe as what would come out of the best practices, then you’re allowed to get out of the box a little bit. I find instead the specifications by law approach a little stifling of creativity and new solutions.
There are other aspects in the practicality of actually going from design to fabrication to erection to the construction of things, mostly because there’s a different relationship I think between designers, fabricators and erectors. In Italy, you see fabricators and erectors being the same entity as opposed to two separate things, and it’s more expected of the engineer to design the connection rather than the fabricator. Whereas here in the U.S., they’re pretty separate figures who actually do the three different things among design, fabrication and erection. They have touchpoints, but not necessarily a lot. I think that the best outcomes really happen when everyone collaborates from day one.
Q: What’s a piece of advice you’d like to give your engineering students?
A: My piece of advice is to not focus so hard on the GPA but focus on learning as much as you can while you’re in college. Take more classes. Who cares if it’s a difficult class and it’s going to take your GPA from 4.0 to 3.8? The employer is certainly going to look at a GPA, but they’re going to be interested in the fact that your transcripts list classes that are not on the basic requirement list. You can learn more about how to conduct a business, how to code, and have a better programming background for what you do. I know several engineering firms that actually hire programmers to help their structural engineering design workflow, so do not be afraid of taking a class because it’s hard. Your ultimate goal should be learning, earning a degree is just a consequence of that.
Q: What’s one key idea young engineers should take away from this interview?
A: One thing is that we can’t provide them with all of the coverage we would like to in the undergraduate experience. Especially going into structural engineering, I would certainly recommend considering staying on for a master’s degree. During a master’s degree, we also cover topics we would’ve liked to have covered in the undergraduate degree, but there aren’t enough credits to cover everything. We also cover the why — not just the how — of a lot of structural engineering applications. I think it makes them better problem solvers and makes them better engineers in terms of being able to tackle something that doesn’t have a cookie-cutter solution.
The other is to work closely with their supervisors, but also to not be afraid to continue learning things on their own because there’s always something new to learn and to get a better understanding of. Never stop learning.
Round HSS Bolted End-Plate Connections under Axial Tension Loading
Read how splicing HSS members in tension together with a bolted connection can be a far simpler and more economical solution compa…
Webinars On Demand: Bolting to HSS
This free webinar teaches various bolting techniques for HSS connections, gives details and design examples and more.
Hidden Bolted HSS Splices
Learn techniques tools, and aesthetic benefits you can achieve when using hidden bolted splice connections between HSS members.