WF Beam-to-HSS Column Moment Connections Using Laser-Cut Columns
In this article, “WF Beam-to-HSS Column Moment Connections Using Laser-Cut Columns,” Professor Jeffrey A. Packer explores how laser cutting technology is revolutionizing the fabrication process by enabling high-precision cuts that are both rapid and cost-effective. The article delves into various connection methods, from traditional welding to the introduction of laser-cut slots, I-shaped openings, and through plates. Laser cutting facilitates intricate designs and superior fit-ups. The research extends to connections using through plates and beams, shedding light on their performance under different loading conditions. With a focus on practical applications and design principles, this article positions laser cutting as a transformative force in advancing the efficiency and strength of beam-to-column connections.
By Jeffrey A. Packer
Bahen/Tanenbaum Professor of Civil Engineering, University of Toronto, Ontario, Canada
December 2023
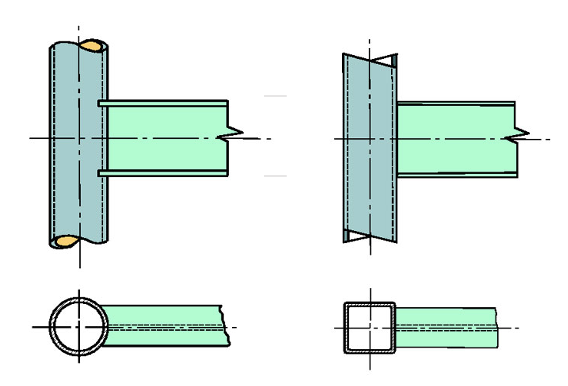
A connection with limited moment capacity, between a wide flange beam and an HSS column, can be achieved by simply welding the beam end directly to the face of the column. Such a connection is only partially restrained (PR) or semi-rigid, due to the inherent flexibility of the HSS column face. Furthermore, for a round HSS column, the end of the wide flange beam will have to be profiled to fit the circular column shape (Figure 1).
In order to achieve a fully rigid moment connection that develops the moment capacity of the beam, one must stiffen the column cross section with plates so that the column maintains its shape. Two common solutions are shown below. In Figure 2, the HSS column is cut into three pieces and re-connected in the shop by welding in two transverse plates, above and below a short HSS stub, as well as shear tabs or angles to resist the beam shear reaction. With the plates slightly wider than the HSS, this can all be achieved by fillet welding. Then, in the field, a site-bolted connection can be made by bolting the wide flange beams to the various plates as shown. This moment connection is popular for frames dominated by gravity loads.
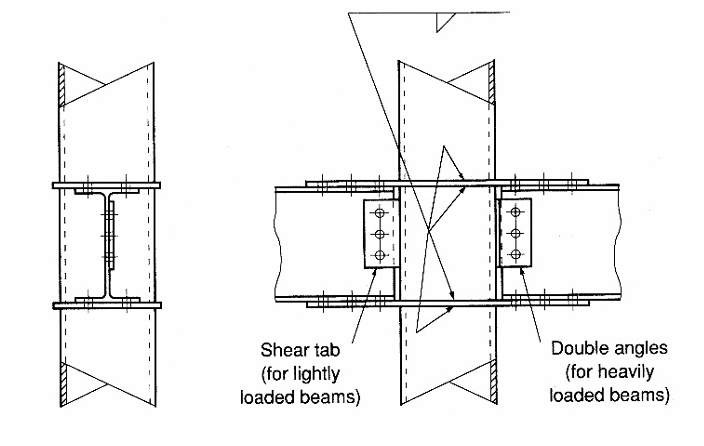
In Figure 3, specially shaped diaphragm plates are slipped over the intact HSS column and shop-welded to it, at the approximate level of the beam top flange and beam bottom flange. These plates surround the HSS column and maintain its shape, and also have a web welded between the upper and lower diaphragm plates. Then, in the field, a site-bolted connection can be made by bolting the wide flange beams to the protruding plates (lower right photograph). If the inflection point in the bending moment diagram is well known, the “beam stubs” protruding from the column can be joined to the main beams at this point of contra flexure (lower left), theoretically using just a shear connection. This moment connection is popular for frames dominated by seismic loads.
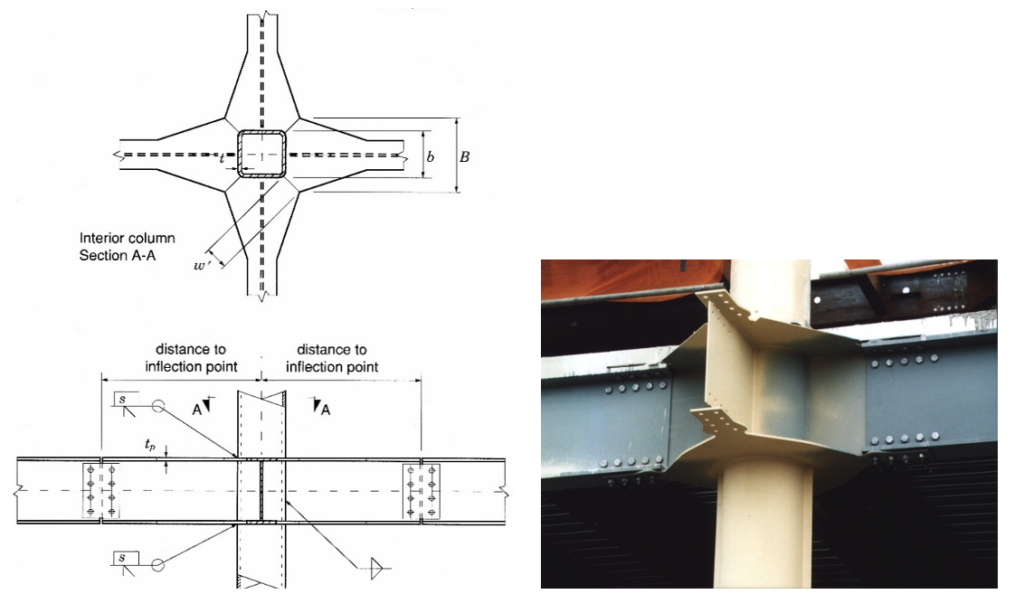
Fabrication using Laser Cutting
The introduction of laser cutting technology to steel fabrication has enabled high-precision cuts to be performed quickly and economically. It is thus possible to cut slots accurately in an HSS member, on opposite sides, so that transverse through plates can be easily fitted through the member and fillet-welded to the HSS on opposite sides. Alternatively, complete I-shaped slots can be easily cut in the HSS member, so that a complete wide flange beam can pass through the HSS (Figure 4). By welding the beam to the HSS, on both sides of the HSS, the complete cross section of a column will be engaged, even if the wide flange beam protrudes only marginally past the far face of the HSS (e.g. for a one-sided connection to an exterior column). Under beam moment loading, such a one-sided connection has a considerably higher available strength than that shown in Figure 1. For a two-sided moment connection, a beam stub could be passed through the HSS column (Figure 4 – right), welded to the outside of the HSS on opposite sides of the member, and then the main wide flange beams could be site-bolted to these protruding stubs. Figure 5 illustrates the excellent fit-up that can be achieved by laser cutting, which significantly aids the subsequent welding.
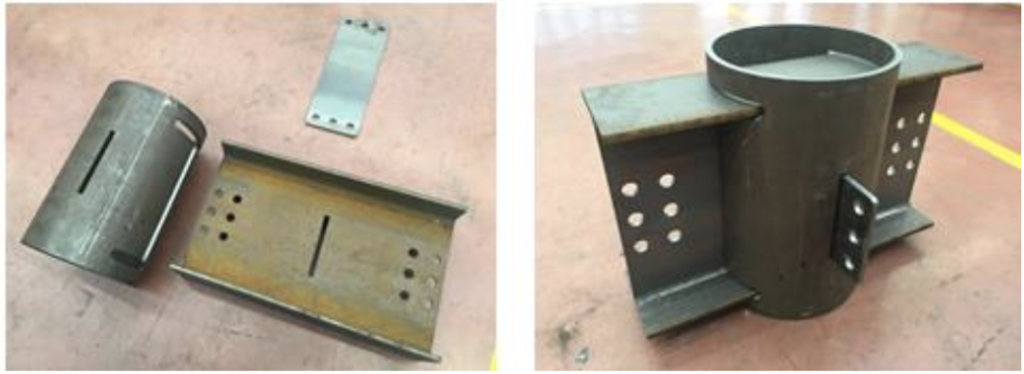
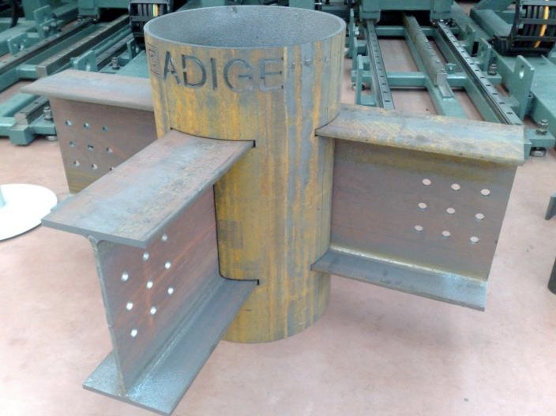
Beam-Column Connections using Through Plates
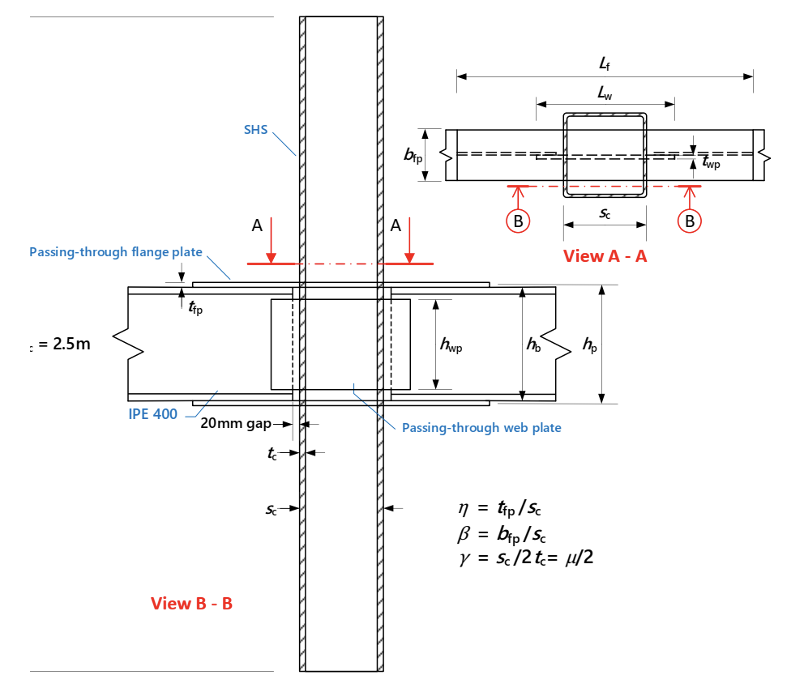
There are instances where it may be impossible or impractical to pass a wide flange beam through an HSS column, such as when the beam flange is wider than the inside diameter or width of the HSS column. In such cases, single transverse plates can be passed through the HSS, welded to the outside faces of the HSS, and subsequently site-bolted to the beam flanges. In order to enable shear force transfer and to maximize the moment capacity of the connection, a third longitudinal (web) plate is also passed through the HSS, welded to the outside faces of the HSS, and subsequently site-bolted to the beam web. This is illustrated schematically in Figure 6. The performance of this connection type has been studied for two beam moment loading cases: (a) beams loaded by equal and opposite (self-equilibrating) moments, as produced by gravity loads; (b) beams loaded by equal moments (in the same direction), as produced by lateral loads.
Beams loaded by equal but opposite moments
For this loading condition, the connection capacity is typically governed by the compressive capacity of the through plates, particularly the compression transverse through plate, which buckles within the HSS. This is illustrated by numerical simulation (finite element analysis) in Figure 7. Thus, the size of the through plates is crucial for this type of connection and loading. This was found to apply for both rectangular and round HSS columns (Madhouni et al., 2023a).
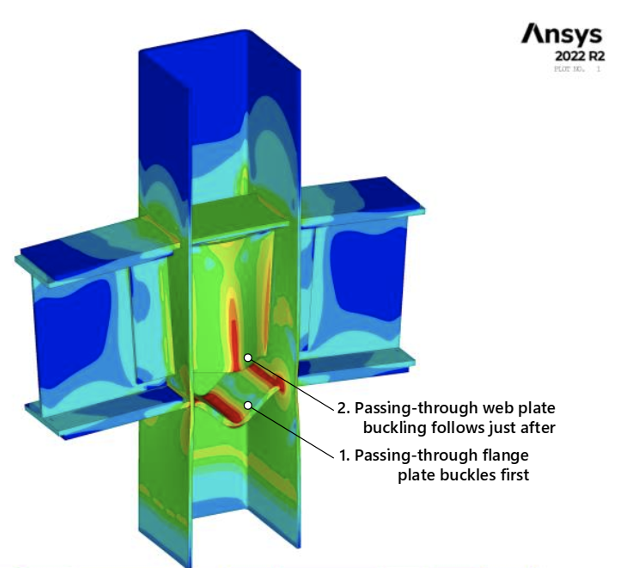
Beams loaded by equal moments in the same direction
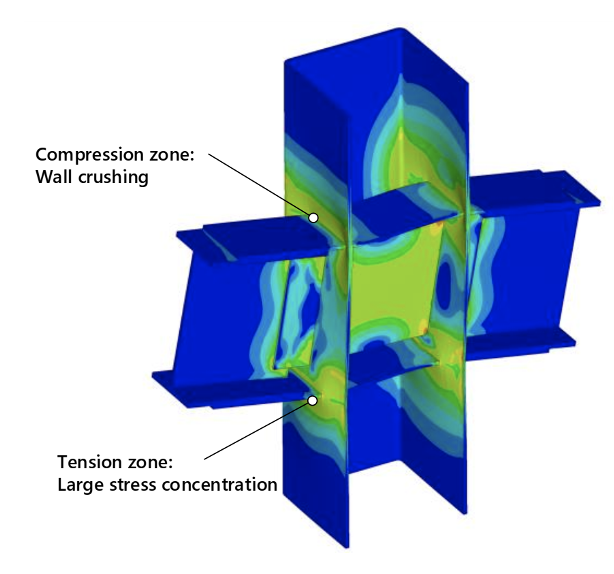
For this loading condition, the connection capacity is typically governed by failure of the HSS wall in the plate-to-HSS welded joint region: by yielding then rupture in the tension zone, and by local yielding in the compression zone (Figure 8). Thus, each transverse plate acts as a through-plate connection under the combined axial load applied to the plate. The HSS wall thickness is therefore crucial for this type of connection and loading. This connection behavior applies to both round and rectangular HSS (Madhouni et al., 2023b), and would also apply to a single-sided beam connection to an HSS exterior column. The capacity of a through-plate connection, welded to the near and far sides of an HSS member and subjected to axial load in the plate, is not covered in either the AISC Specification (AISC, 2022) or the Manual (AISC, 2023), but the available strength of a through-plate connection under axial plate load is now covered in AISC Design Guide No. 24 (Packer and Olson, 2023), in Table 8-1 (for round HSS) and Table 8-2 (for rectangular HSS).
Beam-Column Connections using Through Beams
By passing the beam member through the HSS column, and welding it in place to form protruding beam stubs, the three “through plates” become integrally connected and thereby stiffen each other. The strength and stiffness of the connection with three through plates is hence a lower bound to the connection with a through beam. Thus, at this stage of research on this topic, the through-beam connection could be designed in the same manner as the connection with three through plates. This is clearly conservative, and it has already been found that the flexural capacity of the beam can often be attained with a through-beam single-sided moment connection to an HSS exterior column (Das et al., 2023).
References
AISC. 2022. “Specification for Structural Steel Buildings”, ANSI/AISC 360–22, American Institute of Steel Construction, Chicago, IL.
AISC. 2023. “Steel Construction Manual”, 16th edition, American Institute of Steel Construction, Chicago, IL.
Das, R., Kanyilmaz, A., Madhouni, M. and Degee, H. 2023. “Innovative One-Way Connections between I-Beams and CHS Columns”, Eurosteel 2023, Amsterdam, The Netherlands, Proceedings (Ernst & Sohn) ce/papers Vol. 6, No. 3 – 4, pp. 1539 – 1544.
Madhouni, M., Couchaux, M., Hjiaj, M. and Kanyilmaz, A. 2023a. “I-Beam-to-SHS-Column Moment Resisting Joints using Passing-Through Plates under Equal Loadings”, Eurosteel 2023, Amsterdam, The Netherlands, Proceedings (Ernst & Sohn) ce/papers Vol. 6, No. 3 – 4, pp. 1445 – 1450.
Madhouni, M., Couchaux, M., Hjiaj, M. and Kanyilmaz, A. 2023b. “I-Beam-to-SHS Column Moment Resisting Joints using Passing-Through Plates under Opposite Bending Moments: Numerical and Analytical Studies”, Eurosteel 2023, Amsterdam, The Netherlands, Proceedings (Ernst & Sohn) ce/papers Vol. 6, No. 3 – 4, pp. 1451 – 1457.
Packer, J.A. and Olson, K. 2023. “Hollow Structural Section Connections”, Steel Design Guide No. 24, 2nd edition, American Institute of Steel Construction, Chicago, IL.
The Cutting Edge of Fabrication: Laser Cutting HSS
In our exclusive interview with Mark Mercurio, the regional sales manager at Mazak Optonics Corp., Mark provides valuable insights into the world of 3D laser-cutting machines, with a spotlight on Mazak's 3D FABRI GEAR 400 III. Read the full interview for insider perspectives on how fabricators can harness the power of HSS laser cutting, speed up timelines and increase accuracy.