Overcoming Challenges to Open New Levels of Communication and Structural Possibilities
Peer Perspective: Brian Volpe, Chief Engineer of Cives Steel Company and Cives Engineering Corporation in Alpharetta, Georgia
We recently spoke with Brian Volpe, chief engineer of Cives Steel Company and Cives Engineering Corporation. With a varied background and a deep bench of experience across consulting and fabrication, we touched on topics including effective communication strategies, overcoming common challenges and the evolution of the steel industry as we look to the future.
Q: Can you share an overview of your professional background and tell our readers what you’re up to today?
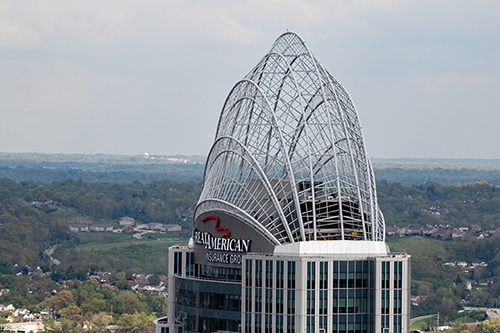
A: Sure. I’m currently the chief engineer at Cives Steel Company. I’ve been in the steel industry since 1995, and I started my career as a steel detailer for Ross Steel, a fabrication shop in Detroit, Michigan. I earned my BS in civil engineering and a BS in architecture from Lawrence Technological University in Southfield, Michigan. In 1999, I started my professional career with Ruby and Associates — a great engineering firm in the metropolitan Detroit area. My project work was highly involved in the steel industry, including erection engineering, connection design and value engineering studies. I also gained my early experience there in advanced workflows that streamlined the process from design to fabrication. In 2008, I joined Thornton Tomasetti and worked in their Chicago office. My role at Thornton Tomasetti was to help continue the development of the service sector they now call construction engineering. My primary focus was to help bridge the design and construction process by developing 3D digital models, in concert with the EOR design team, with fully developed connections that were ready for the fabrication process. I was fortunate to work on many complex structures and installation procedures during my time with Ruby and Associates and Thornton Tomasetti.
In 2016, I joined Cives Steel Company as the chief engineer. I oversee engineering, and I’m the registered professional engineer covering all the states we do business in. My primary role is to provide our seven steel divisions with technical and professional support as needed to support their business. I am also in charge of the engineering division Cives Engineering Corporation (CEC). At CEC, we also perform project work, connection design and other steel engineering duties. CEC is also heavily involved in ongoing support of various AISC technical committees.
Q: You have experience working in the steel connection design office and an EOR office, and now with fabricators. So is there a communication strategy between EORs, connection engineers and fabricators that you found leads to greater success? Are there any best practices to share?
A: Communication is probably the most essential thing we need in this industry right now. I think the last 18 months have intensified that, but I think the challenges are the same now as they were 20 years ago. It’s a question of how do we create viable technical solutions for complex structures? That’s the end goal.
The EOR has their role in providing documents that outline the geometry, the member shapes and material grades, and the forces. The fabricator must take all of that information and develop the solution into shop drawings that can be responsibly submitted for approval. Eventually, the erector and the general contractor have to put the building together in a way that addresses all the technical issues. Making the technical information readily available is certainly a challenge. The EOR needs to make sure that the load path, lateral system and forces are defined and any delegated scope of work is communicated in the design drawings and the specifications so the delegated design engineer is capable of performing their scope of work successfully for the project.
Compared to 20 or 30 years ago, there is often much more information available and there are also potentially digital exchanges of information that can be utilized. Another challenge in our industry is organizing that information in a viable way so it can be pared down and reasonable solutions can be developed that cover the project scope.
Q: What’s an effective method you’ve seen on projects to communicate connection forces to delegated connection engineers?
A: What’s important is to make sure that the connection information needed to perform delegated work is outlined for all of the scope that is required. Probably the largest breadth of connections that need to be delegated are simple shear connections. I’m a fan of reasonable beam schedules that have a reasonable reaction up to a certain limit, and then all other beams exceeding that shear value are actually shown on the plan. I know a lot of engineers and fabricators like every force to be shown on every beam — that’s certainly a viable method as well. Moving past the simple connections, the most important thing is making sure that the more complicated connections have the shears, axial transfer forces, moments and other forces documented properly in a way that the delegated task can be performed.
Q: Could you describe a notable HSS project you worked on in the past?
A: I’d like to talk about the Queen City Square project in Cincinnati. My role was working on the tiara, which is the structure on top of the 41-story building. It was all HSS tubes. I recall the tubes were between 4 inches and 20 inches in diameter. At the time, I was with Thornton Tomasetti, and we were the EOR for the whole building, including the tiara. What was interesting about this project was it evolved over a number of years. Gyo Obata had drafted this up many years prior, and the top of the building was inspired by Princess Diana’s crown as I understand it.
There were a lot of initial sketches to turn into 3D structural models. Eventually, the 3D structural model was sort of the key geometric information on the structural drawings. But we had to turn this into a geometry that could be fabricated and make sure we captured the look the architects envisioned, and also construct it 41 stories up. The tiara structure is primarily an axial loaded structure. So from a technical perspective, there were a lot of axial transfer forces. There were several challenges we had to go through to get the structure connected, including reviewing all the various HSS wall limit states as we developed the solution.
Q: In your opinion, what are some challenges with connections to HSS members and how have these issues been overcome on some of your projects?
A: The biggest technical issues any engineer and fabricator must work through have to do with local wall strengths, specifically related to axial forces and transfer forces on HSS members. The challenges have a lot to do with the members that are specified during design. I think the bigger challenge is oftentimes, the technical considerations having to do with connection design aren’t really considered enough during the design process. What happens for a lot of structures like pedestrian bridges, which are often built out of tubes, the designer will create a structure that is structurally viable in a 3D analysis software and the members will be specified for strength and will oftentimes show a lot of reserve. However, in the end, the wall thicknesses are not adequate to transfer the axial loads either through the face of the wall or through local wall buckling or any of the other limit states that are other concerns.
Usually what has happened in my experience is you get into the development of the connection design solutions, and the connection designer and the EOR end up in a conversation to try to address the lack of wall strength to transfer the connection forces. Either one of two things will happen: local reinforcement will happen and/or suggested modifications to the shapes will occur. Oftentimes, steel structures have architectural constraints. Understanding those constraints is also important and should be well documented. If I had one piece of advice to share, it would be that the EOR focuses on chords and collectors and make sure these elements have adequate wall thickness to receive the loading from the branch members.
Q: How have you seen the steel connection industry evolve over the years? And do you have thoughts on where you would like to see it head?
A: From a standpoint of evolution, we have more software-based solutions now and fewer hand calculations are being prepared. I think that the connection design industry has been behind mainframe design in that aspect, but I think there are a number of software applications being developed that will help with these solutions. This is good as there are more limit state checks required now than in the past. The research on HSS and the use of HSS has given the industry a lot of information related to the local limit states that need to be addressed. Now, EORs are either performing their own connection design as a practice or on the flip side they are not evaluating these limits at all. I think there’s more disparity now than there was 20 years ago when fewer EORs were performing their own connection design. I think that more engineers being involved in the connection design is better for the industry and better for a general understanding related to how to get the structure designed and specified.
There’s also more data available to us now. A good friend of mine used to say paralysis by analysis. Sometimes there’s probably too much data. I think where I see the industry continuing to develop is probably more automation for simple connections and potentially with options. Shear only, beam to beam, beam to girder, girder to column — if you go back, the topic of delegated design having to do with fabricator preference is an age-old discussion in the industry. However, I think we’re getting closer to where simple connections could be cataloged in a way that would allow for large libraries of solutions to be available without a lot of engineering or reengineering that is required to be performed.
Overall, I would like to see more training related to this at the collegiate level. I think our undergraduate studies don’t address connections in a way that’s meaningful. A lot of our young engineers are coming into the marketplace and they’ve never even thought about this issue.
Q: Any other grains of knowledge that you’d like to share with our readers?
A: Related to HSS, HSS connections are tricky and require thought. Sometimes, these get specified because of an architectural aesthetic interest. If that is the case, I would encourage the architect and engineering team to invest time during the design to work on indicative details to suit their vision and communicate the architectural constraints. HSS structures — as with all structures — need to focus on load path, and the documents need to communicate these load paths in a viable way if the engineer is going to delegate the connection design effort.
Design Guide 24 and the HSS Design Manual Volumes 3 and 4 have a slew of great information. They should be almost required reference manuals in a design office and in the fabrication office. Combined, HSS Design Manual Volume 3: Connections at HSS Members, HSS Design Manual Volume 4: Truss and Bracing Connections, and AISC Design Guide 24: Hollow Structural Section Connections have over 470 pages of reference information, charts, example problems, et cetera. Each of them has good high-level information that allows engineers who may not do this every day to get more in tune with some of the technical issues that are going to need to be addressed on their projects regardless of their current depth of knowledge.
HSS Design Manuals
HSS Design Manuals incorporate AISC 360-16 Specification and current HSS shape availability.
HSS Connections with Rotated Members
Architects are continually exploring ways to make interesting and aesthetic structures with HSS. One way is to rotate square HSS b…
Explore HSS Connex
HSS Connex online gives designers a simple way to check HSS wall thicknesses to aid in efficient HSS connection design. You can get a free 30-day trial or gain unlimited access through an HSS Professional Membership.