HSS Damage Due to Water Infiltration and Freezing
By Kim Olson, PE
Technical Consultant, Steel Tube Institute
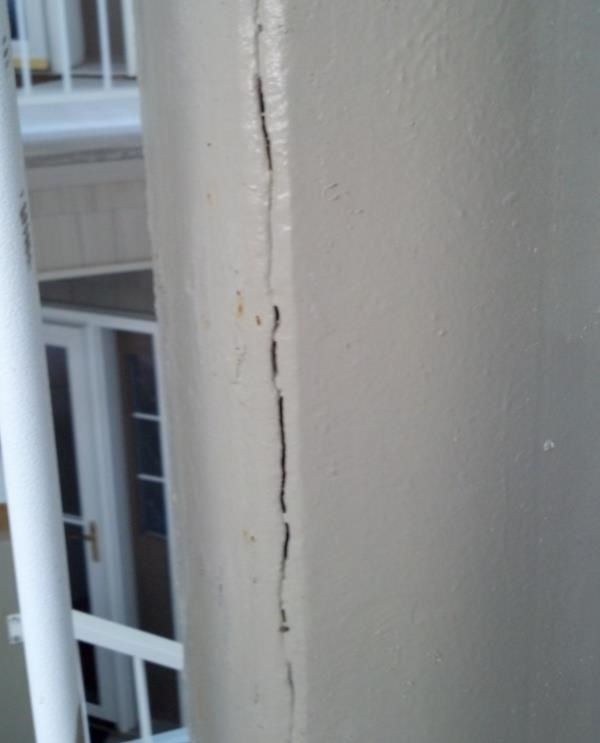
Much of the United States has experienced freezing temperatures this winter–even areas where that isn’t the norm. With that, the Steel Tube Institute (STI) has received a few calls pertaining to water-filled HSS sections that have frozen and been damaged from the water expanding.
Often, for HSS exposed to weather, we specify a weld all around at the cap and base plates. Although this is a good start, this doesn’t always mean the assembly is watertight. The continuous welding of the HSS seam and around the member at cap and base plates does not necessarily produce a complete, watertight seal. There is always the possibility of pin holes or micro-cracks in the member or at connections that may allow moisture to seep into the cavity of the HSS. Water can be drawn into the HSS by capillary action through these micro-openings when a relatively warm HSS is cooled by rainwater. If there is no path out for this water, it will remain in the cavity of the HSS, possibly building up over time, and then expanding under freezing temperatures. The HSS may not be able to restrain the bulging resulting from the ice.
For that reason, STI recommends specifying a small weep hole at the base (or underside if a horizontal member) of the member, in addition to closing the section with cap and base plates. This small weep hole will allow any moisture that enters the section during construction or service to have a path out. If the member is galvanized, this weep hole can do double duty as a vent hole for the galvanizing process.
If these preventive measures have not been followed at the forefront of a structure’s life, it is possible that damage may occur as the moisture freezes and expands inside the cavity of the HSS member. Typically, a crack will propagate from a corner as this portion of the section is highly stressed from the forming process. The repair necessary depends on the loading of the member.
Before performing repairs, ensure that all water is removed from the HSS or a weep hole installed.
If the member is in pure compression, a structural repair is likely not necessary. The same amount of material is still present and continuity of the shape around the corners is not required for compression. It may be prudent to stop the propagation of the crack by gouging and then re-welding the crack.
If the member is used in bending (or compression and bending), gouging out the cracked area and then re-welding it back together, preferably using pre-heating, is one option. Then, it is usually a good idea to strengthen the area locally. For this, I have seen an angle fitted to the corner of the section and welded into place. If the crack is not at the corner, a cover plate can be added. This reinforcement will ensure that the member behaves as a closed section and the addition of more steel will locally enhance the cross-sectional properties.
This issue is addressed in AISC 360-16 “Specification for Structural Steel Buildings” Section M2.10. It states, “Drain Holes – When water can collect inside HSS or box members, either during construction or during service, the member shall be sealed, provided with a drain hole at the base, or otherwise protected from water infiltration.” Additionally, Commentary Section M2.10 states, “Care should be taken to keep water from remaining in the HSS during or after construction, since the expansion caused by freezing can create pressure that is sufficient to burst an HSS.”
February 2018