Steel Conduit Tech Talk: How Conduit Prepares You For Change
When planning to construct a new building or expand an existing one, there is a temptation to utilize materials and techniques that initially seem to be more cost-efficient than other methods. However, this thinking is often shortsighted, and the perceived “savings” could end up costing much more in the end. Many buildings today are designed for life spans of 50 to 80 years or more, and the true cost and value of a building can only accurately be determined by the cost of service, maintenance and repairs over its life — and how well it is able to change to keep pace with evolving needs and technologies. The building’s electrical system is a critical part of that consideration, and a well-thought-out design that allows for change and adaptability will retain its usefulness well into the future.
With the ever-increasing pace of technology and the push towards more efficient and environmentally friendly buildings, the need for an electrical system that can readily adapt and keep pace with these advances has never been more important. Installing the electrical and communication system in metallic raceways is the best way to ensure that your facility is prepared for whatever the future might hold. Metallic raceways not only provide the highest levels of safety and protection for the wiring, but also enhance the ability to upgrade, expand, update and repair the facility in
the most cost-effective and timely manner possible.
Following are code requirements that demonstrate the importance of considering total life cycle costs and adaptability when selecting your wiring method.
ENERGY CODE
Voltage drop is becoming a focus of energy conservation because of the loss of electrical energy through heat that is not performing useful work. ASHRAE 90.1 already has requirements for limiting voltage drop (Section 8.4.1-2010). Where conductors are upsized to compensate for voltage drop, the National Electrical Code® requires the equipment grounding conductors to be increased in size proportionally. Cables are generally constructed with a grounding conductor sized for the anticipated overcurrent device, and they may not contain a properly sized equipment grounding
conductor to comply with 250.122(B) if upsized above minimums (see example 1).
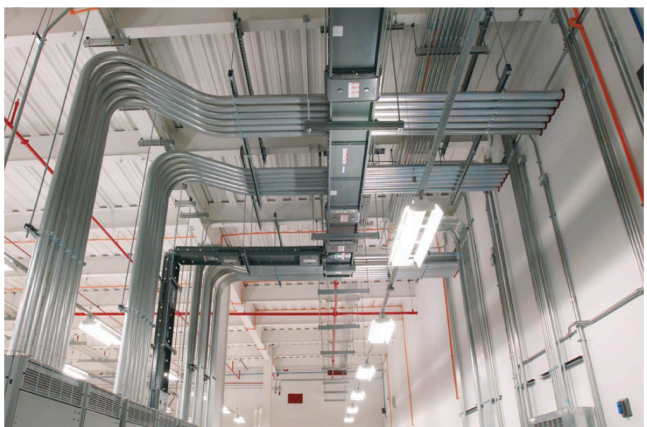
ELECTRICAL CODE
In the 2011 NEC, a new provision was added (404.2(C)) that requires a grounded (neutral) conductor to be installed at each switch location that controls a lighting load. The rationale for this requirement was to address the growing use of occupancy sensors to control lighting, either as prescribed in the energy code, or as a voluntary alteration to reduce a building’s lighting load and cost when the illumination is not needed. Many of these sensors require a grounded conductor connection to the device in order to function.
Many existing switch locations were not provided with grounded conductors. In order to allow the device to function, installers would routinely connect the grounded conductor for the device to the equipment grounding conductor, violating the electrical code, introducing current on the equipment grounding conductor and possibly creating a hazardous situation.
If the initial installation employed cables, installing an additional grounded conductor is not possible: The NEC requires all circuit conductors to be installed in the same raceway or cable.
Obviously, you cannot install an additional conductor in a cable, so the entire cable must be removed or abandoned, and a new set of conductors installed. However, if the installation was originally wired with a raceway, it is a simple matter to install the required grounded conductor. Your facility is now up to date and reducing energy usage. You thought ahead — you were prepared for the future.
The situation with switches becomes even more complex with the use of three-way and four-way switch installations. Because some installations would require four, five and even six conductors to be run from one switch point to another (two “travelers,” a switched conductor, a power conductor, a grounded conductor and an equipment grounding conductor), ordering special cables to accommodate such installations is impractical at best, and not cost-effective under nearly any conditions, especially in small quantities. The initial installation utilizing steel conduit eliminates the need for a wire-type grounding conductor and allows the easy installation of conductors that are needed today and any that might be needed tomorrow.
FUTURE EXPANSION / ALTERATIONS
Expanding a facility usually involves increasing the electrical capacity to serve the additional area and loads. The most cost-effective method of increasing the electrical capacity is generally to leave the existing feeder in place and parallel that with an additional feeder or feeders. Paralleling conductors for expansion require the equipment grounding / bonding conductors to be full-sized, based on the rating of the overcurrent device. Conduit allows for the easy upgrade of that conductor without removing the entire existing infrastructure. Readily available cables have a specific grounding / bonding conductor sized per the anticipated overcurrent device. This grounding conductor will not comply with 310.10(H)(5) if another cable is installed in parallel with the existing cable to increase the capacity. An expansion requiring paralleling with existing cables will require the existing cable to be removed and a new cable, with a larger equipment grounding conductor, to be installed.
Since an oversized grounding / bonding conductor is a special-order item, additional cost and extended delivery times should be anticipated (see example 2).
CHANGES DURING CONSTRUCTION
It is rare for a construction project not to encounter changes or additions during the construction process. By specifying steel raceway, the impact of those changes can be minimized. Often, additional or larger conductors can be installed in the raceway without extensive rerouting or removal of the installation. With cables, it is not possible to add conductors or upsize conductor sizes without complete removal and replacement of the cables, adding significant labor and material costs to the project as well as disruption of the schedule. Steel raceway minimizes the impact of changes and helps your project stay on schedule.
MINIMIZE DOWNTIME
The cost of downtime on productivity, whether manufacturing, financial, service provider or other, is often far in excess of the cost of the repair to the electrical system. This interruption can result from a variety of causes: lightning strikes, worker mistake, aging infrastructure, utility problems, extreme weather, etc., and rarely is there any advance warning. If you have cable, you usually have to remove and replace the entire cable. If that cable is behind the building finish, that portion of the building must be exposed or removed and repaired as well. If that same failure is in conductors installed in a raceway, the cables may be removed from the raceway and new cables installed. There is no need to remove building finishes. The repair is quick and efficient, and your facility is back in operation with minimum disruption, saving not only repair costs, but eliminating a significant portion of costly downtime.
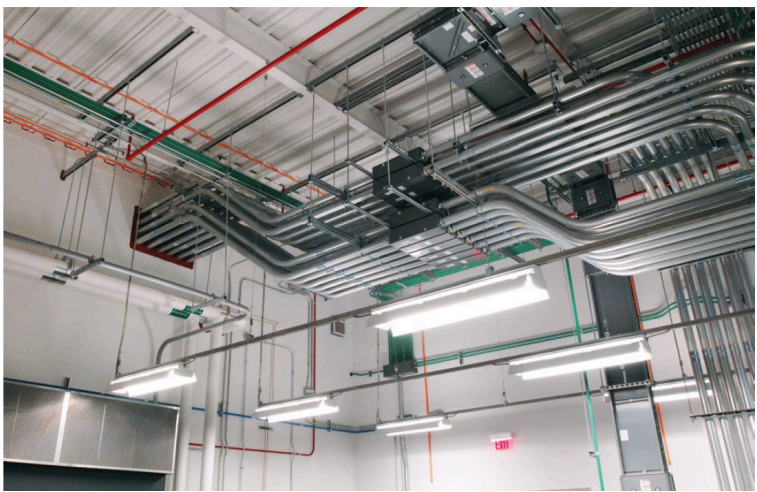
APPENDIX
Example 1
Consider a facility design that calls for a motor that requires a minimum circuit size of 115 amperes capacity. From NEC Table 310.15(B)(16), a size 2 AWG THHN copper conductor has the required capacity. However, because of the length of the circuit, voltage drop will be a problem, so the conductor is increased one size; to 1 AWG THHN copper. Referring to Table 8, Conductor Properties, in Chapter 9 of the NEC, we find that 2 AWG has an area of 66,360 circular mils, and a 1 AWG an area of 83,690 — an increase of 26.1%. This means that any wire-type equipment grounding conductor installed must also be increased by the same proportional amount over the minimum. According to Table 250.122, the minimum-size grounding conductor for our circuit is 6 AWG, based on the size of the overcurrent device (probably 125 amperes). Increasing this grounding conductor by 26.1% tells us that the minimum-size grounding conductor is 33,088 cmil. Per Table 8, the closest conductor with an area of at least 33,088 cmil is 4 AWG at 41,740 cmil. If a cable with 1 AWG phase conductors were chosen for this circuit, the standard grounding conductor would be 6 AWG, which complies with Table 250.122 for a standard circuit, but is not compliant for the upsized circuit. Likewise, if this circuit were installed in a nonmetallic raceway, it would need to be upsized to 4 AWG, possibly requiring a larger-size raceway. Metallic conduits are recognized as equipment grounding conductors per 250.118(2), (3), and (4), so additional grounding considerations or calculations are not necessary. The installation is compliant and your facility is prepared for the future.
Example 2
Take an example of a facility that initially required a 200-ampere feeder to a portion of the facility. Business has been good, and after a few years, it is time to expand, doubling the size of that area. Now a 400-amp feeder is required to supply all the new equipment. If a cable was initially installed as the 200-amp feeder, there is no way to retain that cable and add another of equal size that will result in a code-compliant, safe installation. Why? Because 250.122(F) of the NEC states, “Each equipment grounding conductor shall be sized in compliance with 250.122.” That section bases the size of your equipment grounding conductor on the rating of the overcurrent device protecting the circuit. If the initial installation was a 200-ampere cable with copper conductors, the grounding conductor provided in that cable would be a 6 AWG copper. With the expansion, you need 400 amperes of capacity.
That requires a 3 AWG copper equipment grounding conductor. Installing a cable that is a duplicate of the existing one results in a noncompliant installation since the equipment grounding conductors are undersized. That means removing or abandoning the existing cable altogether.
If cables are to be used for the expansion, they must be special ordered with a larger equipment ground, meaning added cost and probable delays for the special cable to be manufactured. However, if you specified a metal raceway for the initial feeder, it is now just a matter of adding a duplicate feeder in parallel with the first. There is no concern over the size of the equipment ground because the raceway is recognized as the grounding conductor and no calculations or upsizing is necessary. You specified metal conduit upfront; you have a compliant, safe, cost-effective
installation that can be installed in a timely manner. You were prepared for the future.