Meeting in the Middle: Understanding the Sales and Engineering Sides of Bolted HSS Column Splices
Peer Perspective: Brad Fletcher, Senior Sales Engineer With Atlas Tube
Our team sat down with Brad Fletcher, senior sales engineer at Atlas Tube, to discuss his journey from engineer to sales in the steel industry as well as sustainability and what new advancements, like the Shuriken structural nut keeper, he is excited to see with HSS.
Q: Can you tell us about your current role and responsibilities?
A: I’m a licensed structural engineer and the senior sales engineer with Atlas Tube. My main role is to be a liaison between other structural engineers and the steel industry, specifically the HSS industry, helping them understand our products and how to design with them as well as take some of the mystery out of the product line.
Q: Before you were in this role, you had some traditional and nontraditional structural engineering background, right?
A: I graduated from Purdue University and came to Chicago and started working in the engineering world at Sargent & Lundy, which is a heavy industry and power plant design firm. I spent a couple years doing that. I then got into the architecture end of the business working for Skidmore, Owings & Merrill and spent the bulk of my career there and a couple other smaller firms.
After 15 years, I had an opportunity to join the steel industry. I joined a company called Corus, and I was there for about 5 1/2 years. That gave me a view of the steel industry as a whole. Being able to travel to other parts of the world, talk with other engineers, and learn about how other people view steel and design in general all around the world gave me a pretty good world view and perspective.
Because of that job, I got to know people at Atlas. Long story short, they decided that they wanted to have a structural engineer on staff. So now I’m with Atlas and have been here for 11 years.
Q: So you know both sides of the table when it comes to engineers and sales.
A: I think I bring a unique perspective that gives me a lot of credibility when I walk in and say, “Hi, I’m a licensed structural engineer, just like you.” I’m fond of saying, “I speak engineer,” and I think that gives people a lot of comfort and helps them open up. I’m here to help them with ideas and help them flesh them out in a language they understand.
Q: What are a few of your favorite HSS projects you’ve worked on?
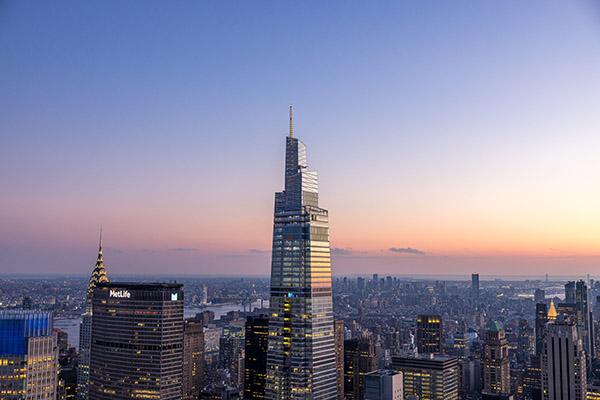
Photo credit: Max Touhey
A: One Vanderbilt, which is a recent project we did a case study on, is a pretty special project. It is a high-rise building in New York that used the jumbo HSS in a way that really created a very welcoming and iconic space in the observation deck and upper part of the building. And this observation deck now is one of the hottest tickets in New York.
Another project I was really happy to be involved with was the Hartsfield-Jackson Atlanta International Airport canopies, design by HOK. These canopies cover the roadways outside the airport. HOK did a fantastic job of designing with round HSS. What’s unique and innovative about this is they use the strength of HSS, not only the beauty, to create essentially cantilever canopies that put very little load onto the existing structure. With other materials, you would’ve had to do a lot of renovation to the existing structure. It was really a great solution.
Q: What are some common pitfalls you see in the field when it comes to designing HSS connections or specifying HSS materials?
A: Understanding the whole connection design aspect of HSS. We as engineers tend to draw stuff and delegate the responsibility for connection design down to the fabricator. We put some typical details on the drawings, and we can tell the fabricator, “OK, here are the loads. You go off and design what works for you.” That’s still possible with HSS, but there’s a lot more attention during design needed, where you have to understand how the HSS is going to react to some of these loads. It’s really more about understanding the limit states and understanding the options that are out there so that the fabricator can be successful.
Q: Are there any key resources you see that STI offers that are helpful to engineers?
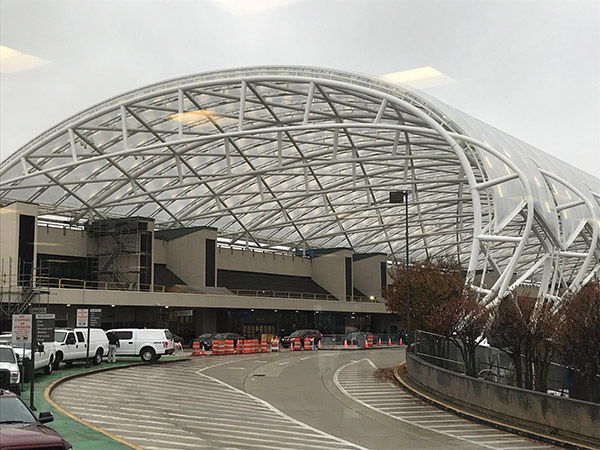
Photo credit: Matt Breindenthal, HOK
A: The HSS Capability Tool that’s on the website. Being able to find who makes what and the availability of some sizes are really key. Also, the design manuals are huge because they updated older design guides. Bringing back all that information and bringing it up to speed has really been extremely helpful to engineers.
Then, of course, the HSS Connex program is great for coming up with the welded connections people use because there’s a lot of mystery behind that and how the code was written. It looks really simple, but it’s really important to understand how it all goes together. Having that HSS Connex program available makes people a lot more powerful.
Q: You have an upcoming presentation on November 30 about HSS sustainability. Could you share your perspective on environmental considerations for HSS?
A: There’s this thought that HSS is going to have more embodied carbon in it than other steel products. The reality is that HSS doesn’t contribute to the embodied carbon of a project any more or less than any other steel products. People think they know how HSS is made. They know it comes from coil, and coil historically has been made by what we call the basic oxygen furnace process or BOF process. The real truth of it is that the vast majority, close to 65%-70%, of the HSS produced in North America comes from what we call electric arc furnaces or EAF coils, which are the more sustainable type of coil. The recycled content for HSS is on par with other structural steel products.
If you look at the data per unit, the global warming potential per unit weight is higher for HSS. But it’s all about utilization. You can show that an HSS will actually end up reducing the amount of total steel in a project, which when you total it all out, it will probably be neutral or potentially even a savings on the embodied carbon.
We’ve been telling people to design as efficiently as possible, then figure out what the carbon is because if you’re pretty efficient, your carbon’s going to be pretty neutral. So, I think that’s kind of the perspective people need to look at.
Q: A development related to bolted splices for HSS columns is the Shuriken structural nut keeper. Could you describe how this product was created?

A: Ted Goldstein, who is the inventor of the Shuriken, approached me a few years ago with this product he developed. He was a young engineer practicing in the United States and had an opportunity to go to Japan with his wife where she was working. The Japanese use a lot of HSS, and they tend to weld everything. He was kind of brainstorming, “There’s got to be a better way to connect these by using bolts.”
And lo and behold, he came up with the Shuriken. Then he came to me saying, “Hey, what do you think my best way to get this into the marketplace is?” I saw it as an opportunity. We solved a fundamental problem people have with HSS, which was just how to connect it safely, cheaply and effectively. And so, now we launched the Shuriken for 3/4 inch and the 7/8 inch bolt sizes, and soon we’ll be launching the 1 inch.
Q: And it was named after a ninja star, right?
A: Correct. If you look at it, it actually looks like a ninja throwing star, and with Ted being in Japan, I think the name came naturally.
Q: Can you list some advantages of the Shuriken then?
A: You use standard bolting technology. You’re using standard A325 and A490 bolts that everyone’s very familiar with. When you have a connection and don’t have access to both sides for bolt installation, the Shuriken solves that by locating the nut on the blind side of the connection in such a way that you can use bolts. Other technologies have solved this problem too, but they’re kind of special. By using standard bolts in standard holes, you’re able to do a little bit more with the connection, and you get to pretension your bolts, if needed. So if you have to do slip critical connections, you can actually get the full required pretension in the bolt. Most people use pretension bolts nowadays in all connections anyway.
Q: What are the best practice applications for the Shuriken?
A: The key thing is that it’s not limited by anything. It’s only limited by the engineer’s imagination. We tend to show it for column splices because that’s one of the obvious places. But we have gone on and developed shear connections and moment connections and post connections. It’s just a matter of finding a creative way of doing a connection such that you can actually use the Shuriken.
Q: Do you have any words of wisdom to impart to younger designers?
A: This is probably a message that other engineers have said, but stay curious and continue learning. Being an engineer is not a static thing. You don’t learn everything in school. Actually, you learn very little in school. You learn most of what you do on the job.
So stay curious and get involved in some part of the industry outside of your company, whether that be one of the structural engineers associations or getting involved with code writing because that opens your eyes to a lot of things. Get out and see job sites. Learning how fabricators do what they do is so important because it’s very easy to sit behind a computer and draw. But if you don’t have a feel for how it actually is going to get built, you’ll never be a successful engineer.
New Concepts for Bolted HSS Column Splices
Dr. Jeffrey Packer reviews two new and innovative concepts for HSS column splicing.
HSS Capability Tool
Need to locate a producer that can manufacture your HSS sizes? Check out our HSS Capability Tool.
HSS Connex
Check HSS wall thicknesses for your HSS connection design. HSS Connex performs the connection strength checks included in AISC 360…