Galvanizing HSS
By Jeffrey A. Packer
Bahen/Tanenbaum Professor of Civil Engineering, University of Toronto, Ontario, Canada
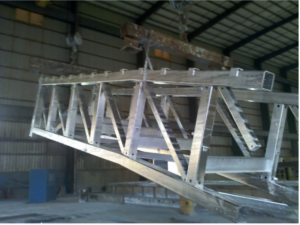
(Photo courtesy of American Galvanizers Association)
AISC 360-16Section B3.13 (AISC, 2016) notes that corrosion of steel components must be addressed where corrosion could impair the strength or serviceability of a structure. Painting, galvanizing and metalizing are popular coating systems used to inhibit corrosion. Hot-dip galvanizing currently represents one of the most effective and economical methods for protecting steel components against corrosion (Figure 1).
Influence of the HSS Metallic Content
With hot-dip galvanizing, the steelwork is immersed in a bath of molten zinc (with up to 2% of other elements) at a temperature around 825 to 870 oF. The average galvanizing kettle is 40 ft. long, although oversized pieces can sometimes be dipped in stages. The zinc temperature and immersion time do influence the thickness of the zinc coating obtained, but one of the most critical factors is the steel chemical composition and in particular the Si (silicon) content. The American Galvanizers Association (AGA, 2006) specifically recommends the following for the dipped steel (HSS), for good galvanized coatings:
(a) C < 0.25%, P < 0.04% and Mn < 1.35%;
(b) Si < 0.04% or 0.15% < Si < 0.22%.
These silicon ranges specifically avoid 0.04% < Si < 0.15%, a zone of high reactivity that generates the “Sandelin effect” in which thicker-than-average zinc coatings will likely be deposited. A500 (ASTM, 2021) and A1085 (ASTM, 2015) heat compositions generally meet these C (carbon), P (phosphorous) and Mn (manganese) limits, but there is no control on Si with A500. A1085 has a Si ≤ 0.04% restriction, which makes it a preferable product for galvanizing. A low silicon content gives a lower carbon equivalent (CE), according to some CE formulas, which has been shown to lower the susceptibility of steel to liquid metal embrittlement (BCSA/GA, 2005).
Influence of the Galvanizing Bath Metallic Content
Aside from the mineral composition of the HSS being galvanized, the chemical composition of the galvanizing bath itself is very important. The reactivity of dipped steel that lies within the Sandelin range can be controlled by adding Ni (nickel). In addition, control of the reactivity of the steel can be assisted by Al (aluminum), Bi (bismuth) and Sn (tin). The addition of Pb (lead), Bi and Sn influences the appearance of the outer layer of the zinc coating, by further improving the drainage of liquid zinc from the surface of the HSS and providing a smooth coating. Al, in turn, protects the zinc bath against excessive oxidation. However, alloying additives can have serious negative effects. The use of galvanizing baths containing Bi and Sn significantly increases the risk of liquid metal embrittlement, and hence cracking of the steel during galvanizing, while Pb is a toxic additive. As a result, recommended ranges for alloying elements in the galvanizing bath have been produced, as shown in Table 1 (Kania et al., 2020). Alternatively, in Germany upper limits are set on Sn, (Pb + 10Bi), Ni and Al content (DASt, 2009). Compared to Table 1, the DASt directive is more strict with regard to Sn content (Sn ≤ 0.1%).

Distortion and Cracking
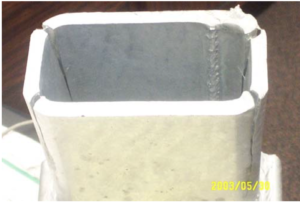
The temperature of a galvanizing bath is very similar to that specified for A1085 Supplementary Requirement S1 for heat-treatment (ASTM, 2015), so stress relief will occur. This should be borne in mind if one is hot-dip galvanizing cold-bent HSS members, for example, as pieces may distort from their bent shape due to stress relief. With galvanizing, the stress relief is very rapid and it occurs in the presence of a liquid metal which typically includes certain additives that exacerbate the situation, as noted above. The heavily cold-worked corners of square and rectangular HSS have a very high level of residual stress and all conditions may exist to induce liquid metal embrittlement of the corners (Packer et al., 2010a; Sun and Ma, 2019), such as shown in Figure 2. Thick-walled, square and rectangular HSS with an open end to the member are most at risk of corner cracking during hot-dip galvanizing (Sun and Packer, 2019).

The galvanizing standard A143 (ASTM, 2020) states that “a cold bending radius of three times the section thickness … will ordinarily ensure satisfactory properties in the final product.” Although the outside corner radius of A1065 (ASTM, 2018) is specified to be three times the wall thickness (3t) or greater, this is the upper corner radius limit for square and rectangular HSS to A500 and A1085. In fact, the outside corner radius of A500 and A1085 averages 2t in practice and this geometry is used for determination of their section properties. Thus, all square and rectangular A500 and A1085 HSS produced in North America are potentially prone to embrittlement and corner cracking during hot-dip galvanizing. Kinstler (2005) pointed out that “… the amount of cold work, as measured by the bending radius, is the most important single factor to consider when there is concern for brittle-type failure of steel galvanized after cold working.”
Before and After Galvanizing
A143 (ASTM, 2020) notes that, for corner bends with a radius smaller than their recommendation (3t), the HSS should be given proper thermal treatment prior to galvanizing. A143 states that “for heavy cold deformation exemplified by cold rolling … subcritical annealing at temperatures from 1200 to 1300 oF should be employed.” A1085 Supplementary Requirement S1 provides heat treatment of 850 oF or higher, so this could be specified for square and rectangular HSS that is destined for hot-dip galvanizing. Cracking in HSS corners during hot-dip galvanizing typically starts from the inside, and grinding the inside corners at open ends of a member has been found to be effective in improving crack resistance. This procedure helps to remove folds and other surface roughness that tend to act as stress raisers and crack initiation sites. It also probably removes some of the hardest and most brittle material at these locations (Poag and Zervoudis, 2003). Trial dipping of HSS member lengths, with a particular galvanizer, is always an option too.
For hot-dip galvanizing, holes to allow for filling, venting and drainage are necessary (see Figure 1), and adequate sizing minimizes differential thermal stresses experienced by the structural component during galvanizing. It is not an option to leave a hollow section member sealed during hot-dip galvanizing as there is a high risk of bursting the HSS. Consequently, the inside surfaces of the HSS will also be galvanized. Vent holes with a minimum diameter of 1/2 in. and drain holes with a diameter of 1 in. are recommended. It has been found that the presence of vent and drainage holes in HSS trusses, such as at the ends of branch members (see Figure 1), does not have a significant effect on the HSS connection resistance (Serrano et al., 2019).
A visual inspection of the corners of square and rectangular HSS, at the member ends, is prudent after galvanizing. However, one must bear in mind that small “invisible” cracks may be present but be masked by filling with liquid zinc. Such cracks may become a problem during the service life of the structure, particularly if fatigue loading occurs. Round HSS, which does not have zones of severe cold forming like rectangular HSS, does not have any concerns with cracking during hot-dip galvanizing. Multi-sided cold-formed hollow sections, such as used for high mast illumination poles (HMIPs), on the other hand, have been found to occasionally crack during hot-dip galvanizing (Nasouri et al., 2019).
Metalizing is another form of coating structural steel for corrosion control, providing protection for significantly longer times than just paint, but it is more expensive than galvanizing. In this process, zinc or aluminum wire is continuously melted and, propelled by compressed air, is sprayed onto the steelwork forming both a barrier and a galvanic coating. The steel remains relatively cool (around 250 to 300 oF) so there is virtually no risk of heat distortion or liquid metal embrittlement.
References
AGA. 2006. “Hot-Dip Galvanizing for Corrosion Protection – A Specifiers Guide”, American Galvanizers Association, Centennial, CO.
AISC. 2016. “Specification for Structural Steel Buildings”, ANSI/AISC 360-16, American Institute of Steel Construction, Chicago, IL.
ASTM. 2015. “Standard Specification for Cold-Formed Welded Carbon Steel Hollow Structural Sections (HSS)”, ASTM A1085/A1085M-15, American Society for Testing and Materials International, West Conshohocken, PA.
ASTM. 2018. “Standard Specification for Cold-Formed Electric-Fusion (Arc) Welded High-Strength Low-Alloy Structural Tubing in Shapes, with 50 ksi [345 MPa] Minimum Yield Point”, ASTM A1065/A1065M-18, American Society for Testing and Materials International, West Conshohocken, PA.
ASTM. 2020. “Standard Practice for Safeguarding Against Embrittlement of Hot-Dip Galvanized Structural Steel Products and Procedure for Detecting Embrittlement”, ASTM A143/A143M-07(2020), American Society for Testing and Materials International, West Conshohocken, PA.
ASTM. 2021. “Standard Specification for Cold-Formed Welded and Seamless Carbon Steel Structural Tubing in Rounds and Shapes”, ASTM A500/A500M-21, American Society for Testing and Materials International, West Conshohocken, PA.
BCSA/GA. 2005. “Galvanizing Structural Steelwork – An Approach to the Management of Liquid Metal Assisted Cracking”, British Constructional Steelwork Association, London, U.K. and Galvanizers Association, West Midlands, U.K.
DASt. 2009. “Guideline for Hot-Dip-Zinc-Coating of Prefabricated Load-Bearing Steel Components”, DASt-Richtlinie 022, Deutscher Ausschuβ für Stahlbau, Düsseldorf, Germany.
Kania, H., Mendala, J., Kozuba, J. and Saternus, M. 2020. “Development of Bath Chemical Composition for Batch Hot-Dip Galvanizing – A Review”, Materials, Vol. 13, 4168.
Kinstler, T.J. 2005. “Current Knowledge of the Cracking of Steels during Galvanizing – A Synthesis of the Available Technical Literature and Collective Experience for the American Institute of Steel Construction”, Report, GalvaScience LLC, Springville, AL.
Nasouri, R., Nguyen, K., Montoya, A., Matamoros, A., Bennett, C. and Li, J. 2019. “Simulating the Hot Dip Galvanizing Process of High Mast Illumination Poles. Part II: Effects of Geometrical Properties and Galvanizing Practices”, Journal of Constructional Steel Research, Vol. 159, pp. 584-597.
Packer, J.A., Chiew, S.P., Tremblay, R. and Martinez Saucedo, G. 2010. “Effect of Material Properties on Hollow Section Performance”, Structures and Buildings, Proceedings of the Institution of Civil Engineers, Vol. 163, No. SB6, pp. 375-390.
Poag, G. and Zervoudis, J. 2003. “Influence of Various Parameters on Steel Cracking during Galvanizing”, Proceedings of the AGA TechForum, Kansas, MO.
Serrano, M.A., Lopez-Colina, C., Gayarre, F.L., Wilkinson, T. and Suarez, J. 2019. “The Resistance of Welded Joints of Galvanized RHS Trusses with Different Vent Hole Geometries”, Applied Sciences, Vol. 9, 1553.
Sun, M. and Ma, Z. 2019. “Effects of Heat-Treatment and Hot-Dip Galvanizing on Mechanical Properties of RHS”, Journal of Constructional Steel Research, Vol. 153, pp. 603-617.
Sun, M. and Packer, J.A. 2019. “Hot-Dip Galvanizing of Cold-Formed Steel Hollow Sections: A State-of-the-Art Review”, Frontiers of Structural and Civil Engineering, Vol. 13, No. 1, pp. 49-65.
December 2021