Architecturally Exposed Hollow Structural Sections
By Cathleen Jacinto, PE, SE
FORSE Consulting, Technical Consultants to the Steel Tube Institute
Architecturally exposed structural steel (AESS) is steel used for its strength and load-resisting function in a structure and remains exposed to view. Since this steel can be highly visible, special requirements and treatment for this metalwork is needed to meet the intent for function and form. Hollow Structural Section (HSS) members are often used in exposed steel applications due to the varied range of shapes offered — round, square and rectangular. HSS walls also create smooth surfaces without the sharp edges of wide-flanged sections. In matched connections, the beam, column or truss member faces can align, which may be desired particularly in frames supporting exterior wall. In addition, HSS shapes allow for the opportunity to achieve “hidden” welded connections, which is advantageous in exposed metalwork.
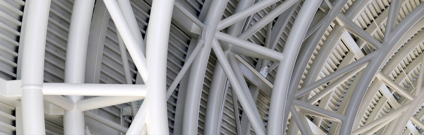
The 2016 Code of Standard Practice (COSP) Section 10 designates five categories of AESS. The categories are selected based on the viewing distance of the steel and the level of finish desired. Table 1 summarizes requirements for each AESS Category.
- AESS 1 – Basic elements
- AESS 2 – Feature elements viewed at a distance greater than 20 feet
- AESS 3 – Feature elements viewed at a distance less than 20 feet
- AESS 4 – Showcase elements with special surface and edge treatment beyond fabrication
- AESS C – Custom elements
HSS sections are produced as cold-formed members using different methods, but one common feature resulting from HSS production is a continuous longitudinal weld, or the weld seam. This weld seam is treated differently depending on the desired AESS category for the exposed steel. Below is a summary of weld seam requirements in HSS members:
- Categories AESS 1 and 2 do not have special weld seam requirements. The weld seams are acceptable as produced.
- For Category AESS 3 where feature elements are viewed at a distance less than 20 feet, the HSS weld seam shall be oriented away from view.
- For Category AESS 4 for showcase elements, weld seams shall be treated so they are not apparent.
- Per COSP Section 10.2, any special requirements for AESS members, such as the orientation of HSS weld seams, shall be indicated on contract documents.
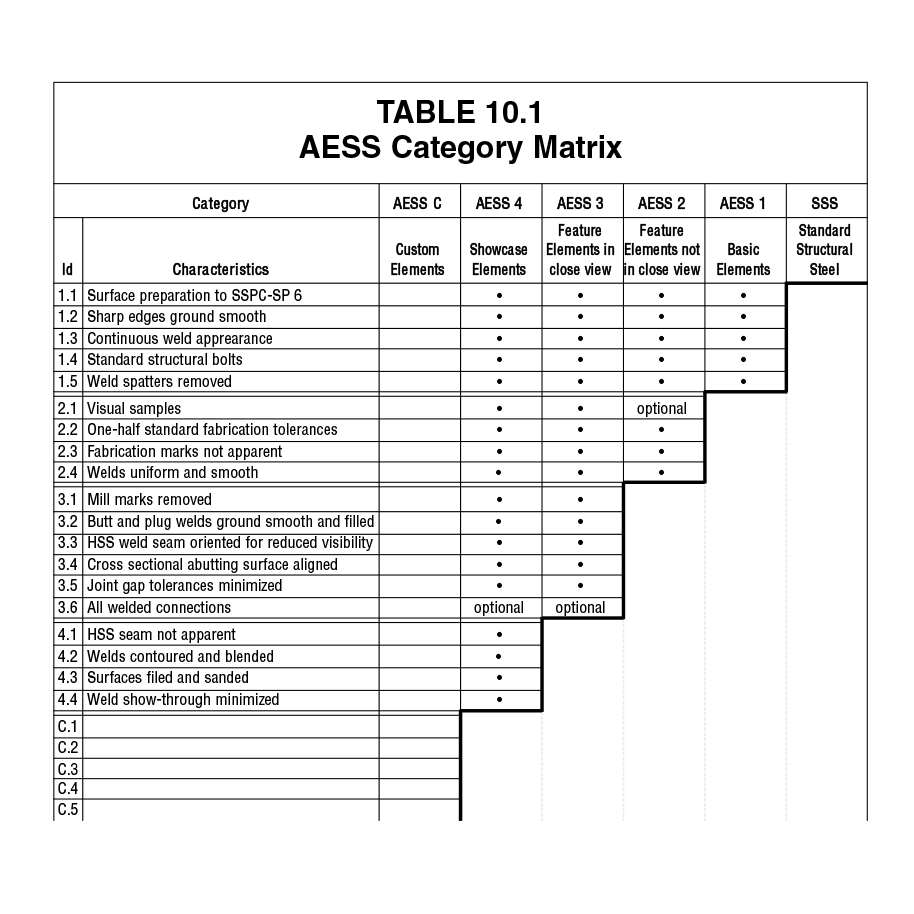
AESS 3 specifies that the weld seam should be oriented away from view. If the piece is visible from all angles, the least-viewed angle should be chosen to locate the weld seam. Given this architectural criterion, engineers would typically not specify the location of the weld seam. However, it is recommended that the design team coordinate this location and this detail be shown on the structural drawings as these documents are typically the primary source of information for the contractor/fabricator to build off of. For Category AESS 3, grinding of the welded seam is not necessary.

rectangular HSS section
AESS 4 specifies that the weld seam in an HSS member should not be apparent. This may require grinding of the weld seam. If it is not feasible to locate the weld seam away from view, then the seams may need to be ground and filled. Note that welded seams tend to remain visible even after grinding of the weld, and grinding weld seams on circular members is very difficult.
AESS 3 and 4 both allow grinding and smoothing of the welds at connections between HSS members, but grinding may not be required. Grinding depends on the complexity of the connection and the expectations. Specifying a mock-up is helpful in determining if grinding can be avoided while still fulfilling the expectations and design intent.
Where two HSS members are butted and joined to ensure that the weld seam locations for both HSS members align with each other, it may be prudent to add a note to this affect on the structural drawings.
It should be noted that not all round HSS are produced with one straight seam weld. Particularly in larger round sections (greater than 16 inches in diameter), members may be supplied to a job with a spiral weld, where a steel coil is unwound and then welded while it is being turned into the shape of a pipe. It is recommended that if larger round sections are being used in an AESS application, the contract document specifies that a section with a straight seam weld be supplied.
In addition to weld seam treatment, below is a summary of additional AESS requirements specific to HSS members. Additional general AESS requirements are summarized in the Code of Standard Practice, Section 10.1
- For Categories AESS 2, 3 and 4, the straightness tolerance for HSS members shall be one-half of that specified in ASTM A6/A6M and ASTM A500/A500M.1
- If a backing bar was used during the production of the HSS section (as in A1065 material) or as part of any connections to the HSS members, all backing bars and runoff tabs shall be removed.
- Contract documents must indicate size and location of vent and drainage holes for HSS members.
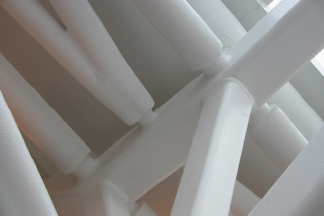
Connections to HSS members should be coordinated with the design team and owner early in the design phase. Good communication is key to avoiding issues or cost overruns during fabrication or construction. Structural engineers and fabricators, once they are on board, can help to make the design team aware of options to connect to HSS. Depending on the connection type chosen, there is the potential for connection end plates or bolts to project outside of the HSS wall. If this is the case, the owner and architect should be made aware to ensure the connection is acceptable for the exposed connection joints. This will also allow for coordination of adjacent architectural pieces, particularly with facade or curtain wall the exposed steel may be supporting. Choice of member type and HSS wall thickness will greatly impact the connection type and any additional reinforcement that may be needed.
HSS contribute significantly to AESS structures due to their form as well as their structural efficiency. Their closed section resists twisting during handling, delivery and erection, and have tighter dimensional control due to tolerances. Therefore, HSS generally make it easier to manage the more restrictive AESS tolerances.
References
- The 2016 Code of Standard Practice for Steel Buildings and Bridges (ANSI/AISC 303-16), Section 10 Architecturally Exposed Structural Steel
- CISC Guide for Specifying Architecturally Exposed Structural Steel by Boake, Terri Meyer, Canadian Institute of Steel Construction, March 2012
May 2019